The video editing and rendering has been tasked to me.
Utilising Robs knowledge has been key, it was his diea to animate the engine being created through wireframe and overlapped with the model.
Once Rob had positioned the lighting and the camera he produced this opening shot.
I had previously learnt from this and replicated it when displaying the spark plug earlier in the blog. Even though I may not have the current knwoledge, I am finding it increasingly important to learn off other group members.
We found that there was a problem with the 2nd stage of the animation. The 2 shots did not line up due to the cameras being miss aligned.
For this I decided that the easiest way would be to rescale the engine to get the dimensions as close as possible to the initial render. Another problem was the shadow in the initial render had been deleted from the 2nd stage.
Before:
After:
By looking closely at the end of before video, you can see that the piston shaft doesn't match up with the Cam. It appears to be rotating on its own.
The group were stumped by this, but after going through the key frames I found that the problem was with the keyframes not aligning, so after a few rotations the shaft moved further and further out of line.
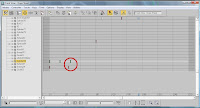
Problem solved:
The next stage was to animate the top of the Piston and to start animating the flow of liquids and gases within the engine.
We decided to use the slice modifier to animate the liquids and used.
This video gives a rough indication of how the piston will be animated. The movement still needs to be fine tuned and textures also have to be added.